Gearboxes with cynapse® and Smart Services
Unlimited Industry 4.0 connectivity: Gearboxes with cynapse® from WITTENSTEIN alpha independently record operating data within machines as well as plants and communicate it in the IIoT. cynapse® functionality is integrated in the existing installation space and is connected via an IO-Link interface.
In combination with our Smart Services, maximum transparency is created within the machine and the Smart Factory, in which the gearbox and process data is recorded and analyzed.
New to our portfolio is the Smart Service cynapse® Analyze – Health Index: It analyzes the drive train data in real time and assesses the actual load on the gearbox to avoid uncontrolled downtimes.
cynapse®
Product identification
The digital name plate provides relevant data for your component’s unique identification.
Data logger
Data is collected and stored throughout your component’s entire life cycle:
temperature, vibration, mounting position and acceleration
Threshold monitoring
Simple monitoring of sensor values based on predefined or individual threshold values.
Smart Services
Intelligent drive train
cynapse® Connect, cynapse® Monitor and cynapse® Analyze capture, visualize and analyze data in the drive train.
Ready to Use
Easy integration into your infrastructure without any programming.
Perfect interplay
Intelligent combination of WITTENSTEIN expertise and your operating data.
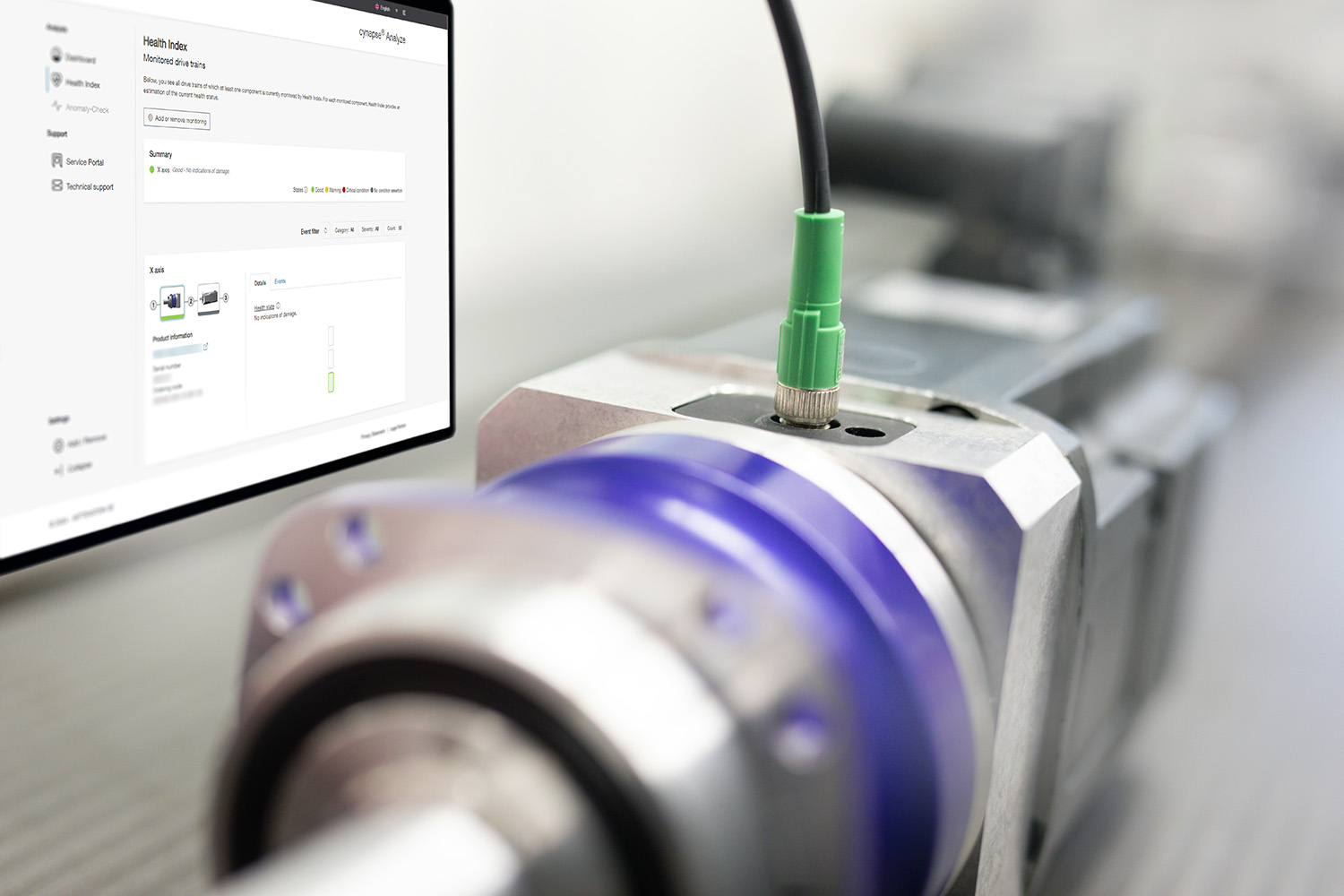
cynapse® integration options
The integration of gearboxes with cynapse® can be categorized into three different integration options:
Internal memory
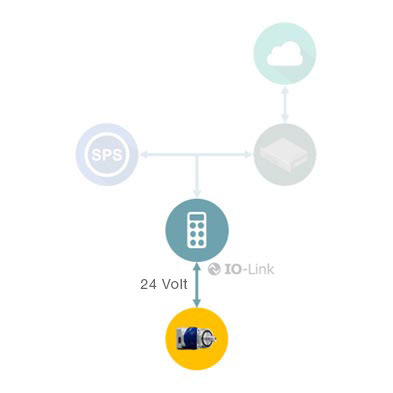
- Use of internal memory
- Storage of data history (e.g. minimum / maximum values & histograms)
- 8 MB memory capacity manages to store data from 40,000 operating hours
SPS Integration
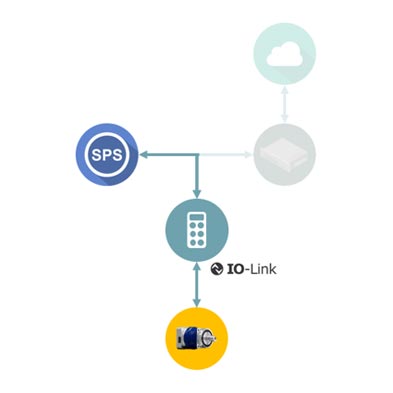
- Integration of cynapse® data and functions into the PLC (e.g. live / process data & IO-Link events)
- Use of cynapse® data for further analyzes
- Data storage in sensor memory still active
IPC / Gateway / Cloud
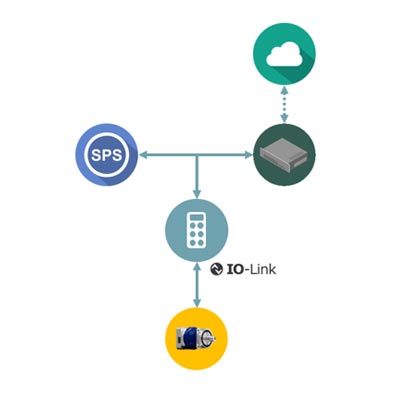
- Integration of cynapse® data and functions into higher-level systems (e.g. live / process data & IO-Link events)
- Use of Smart Services from WITTENSTEIN or further analyzes
- Data storage in sensor memory still active
Smart Services at a glance – NEW: Now with cynapse® Analyze – Health Index
What our customers say about cynapse®
Gearboxes with cynapse® functionality combined with Smart Services are already used in a wide range of machinery and equipment. We regularly receive positive feedback from our customers regarding their experiences. The user report from “KOCH Pac-Systeme” serves as an excellent example.
This is cynapse®
How do cynapse® and Smart Services play together?
Gearboxes with the cynapse® feature and IO-Link interface can be directly integrated into your system landscape. You can decide here whether the generated data is only kept in the cynapse’s internal memory or whether you integrate it into higher-level systems, such as a PLC or gateway/IPC.
By integrating the data into higher-level systems, you lay the foundation to use our Smart Services.
For integration into these systems, we rely on common standards such as Docker or integrate natively into the respective target system such as ctrlX from Bosch Rexroth.
How does digitizing machines and plants work? Our whitepaper provides answers.
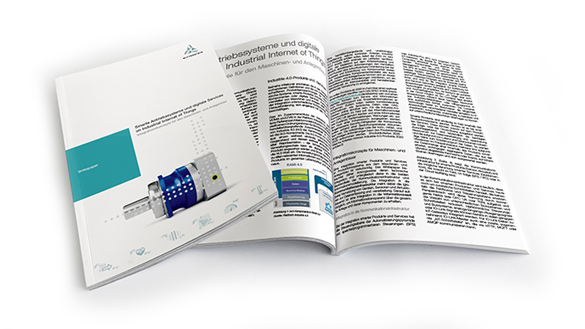
Our smart drive systems and Smart Services enable our customers to successfully integrate their machines and systems into the digital world. Find out in this whitepaper which components can be used for this purpose and what integration into IIoT might look like.
How to succeed with the cynapse® integration: Our Getting Started documents provide answers.
Our Getting Started documents are designed to help our customers integrate cynapse® successfully into their PLC. Our Getting Started documents tell you all you need to know.
Downloads
Kontakt
Is there anything you'd like to know about cynapse®? Do you require personal advice?
If so, please contact us directly. We look forward to hearing from you!